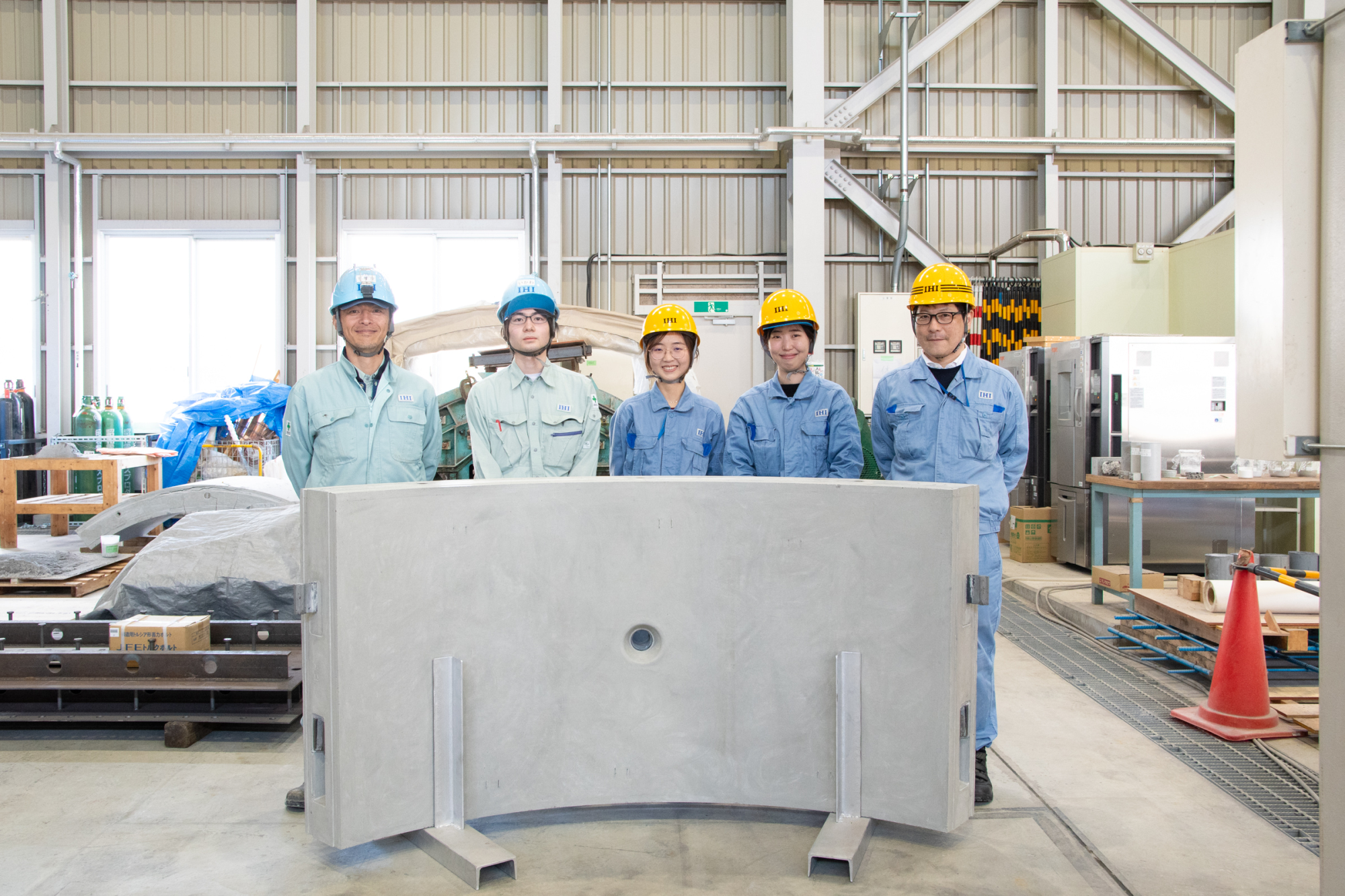
Cement, the main material in concrete, generates a large quantity of carbon dioxide (CO2) in its manufacturing process because of its high-temperature calcination. It is estimated that the amount of CO2 emitted during the manufacturing process would account for 8% of human-caused CO2 emissions worldwide. Given the growing global trend toward decarbonization, the need to reduce CO2 emissions is increasing. In the fields of civil engineering and building construction, the IHI Group has been involved in the construction of many structures including bridges, water gates, tunnels, port facilities, power stations, and various plants. Therefore, we strongly feel obliged to make efforts ourselves to reduce CO2 emissions, with the aim of realizing a sustainable society
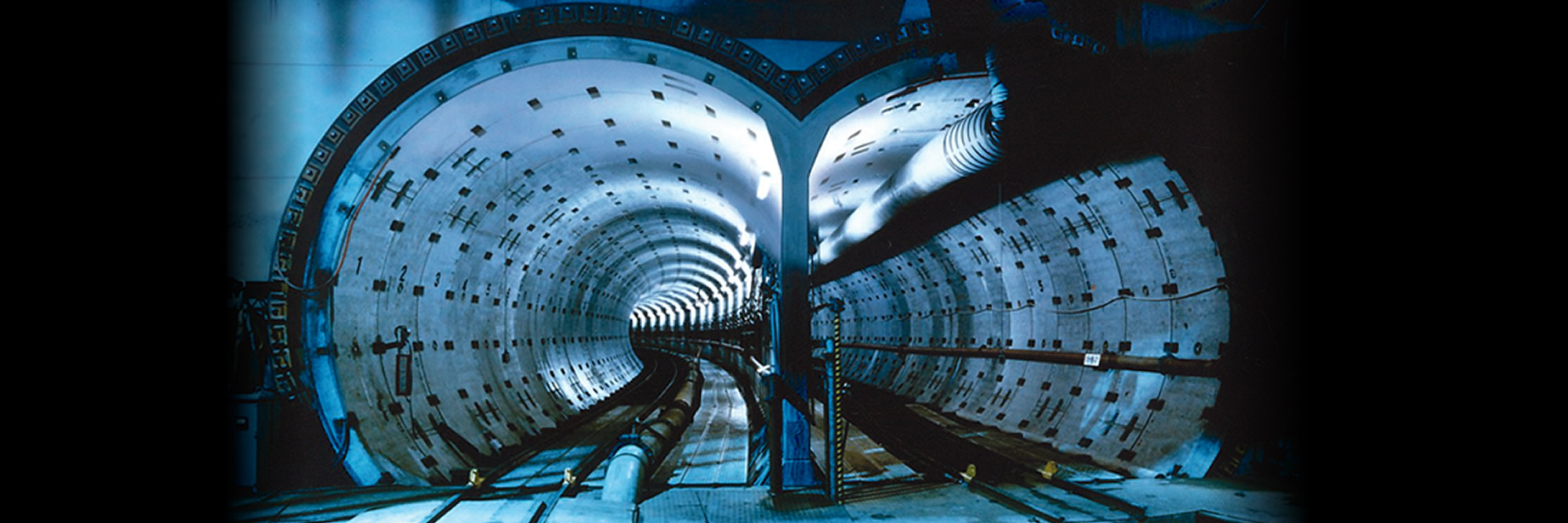
As part of such efforts, the IHI Group has developed CEMENON, a geopolymer concrete that has strength properties comparable to those of cement concrete but that does not use cement, jointly with Yokohama National University and ADVAN ENG Co., Ltd., a company that specializes in the design and fabrication of industrial furnaces and waste treatment plants. The press release was issued in April 2023 announcing the development of CEMENON.
Geopolymer concrete is a construction material produced by adding aggregate (such as gravel and sand) to a geopolymer formed by the reaction of powder containing alkali-reactive material (alumina silica powder) and an alkali-silica solution such as sodium silicate. In Japan, geopolymer concrete began to draw attention in the first half of the 2010s. Amid the mounting calls for decarbonization and carbon reduction efforts in recent years, various companies and research institutions have set out to develop geopolymer concrete.
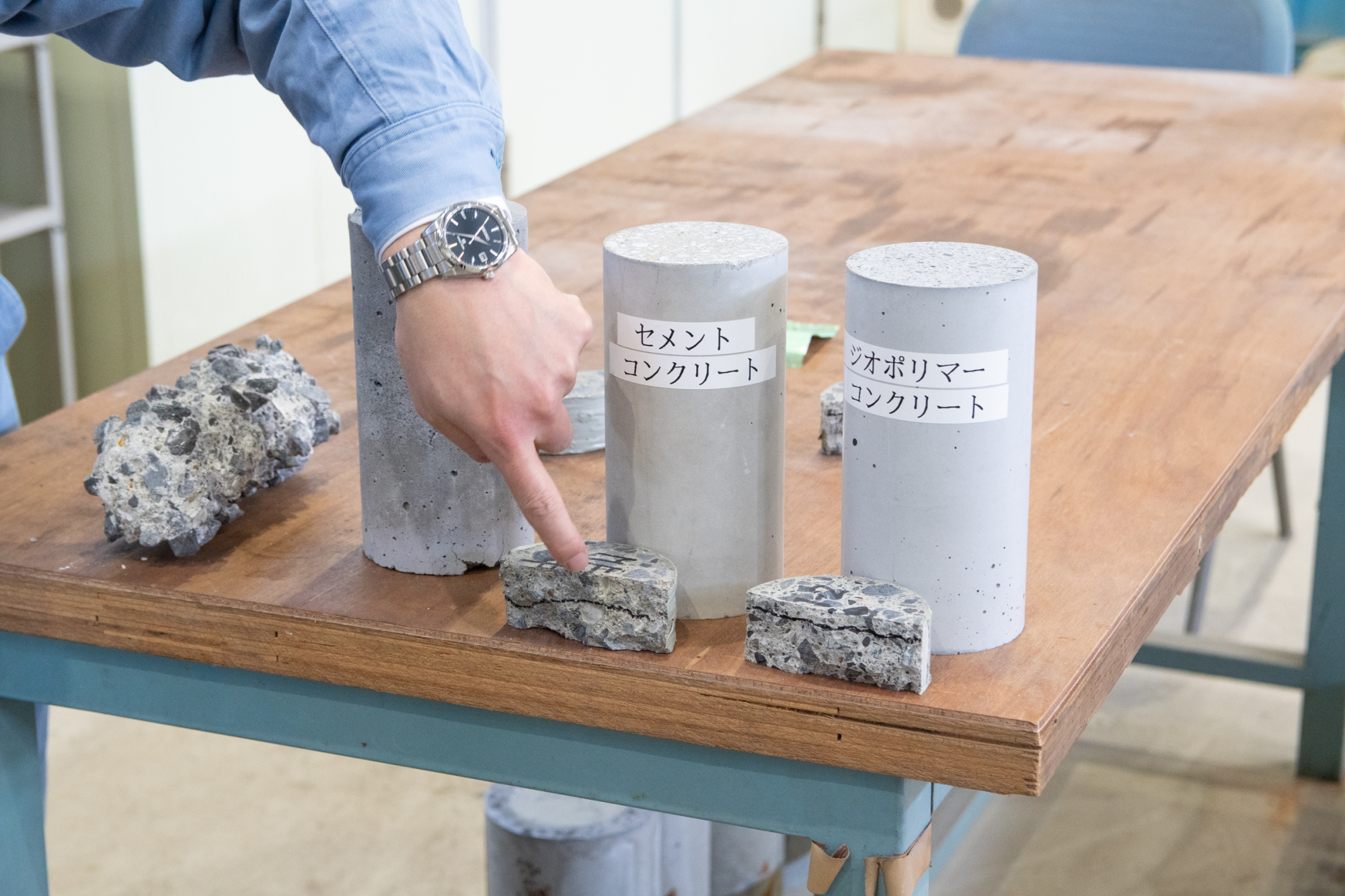
Tomoaki Kisaku, CEMENON development leader in Product and Process Innovation Group, Engineering Department, Integrated Development Center, Corporate Research & Development Division, IHI, has been researching geopolymer concrete since around 2016, having started shortly after the Sustainable Development Goals (SDGs) were adopted by the United Nations in 2015 Kisaku explained: “Though geopolymer concrete was not yet in demand in the civil engineering industry, I started research with the belief that it would someday suddenly become sought after.”
However, things did not seem to be going anywhere, so the research was put on hold. Then, in 2020, the Japanese government declared its aim of achieving carbon neutrality by 2050, and calls to reduce CO2 emissions began to increase. It was in those days that, prompted by the opportunity to work with ADVAN ENG, Kisaku restarted work on the development of geopolymer concrete in 2022. He proposed development collaboration to IHI Construction Materials Co., Ltd. (IKK), an IHI Group company.
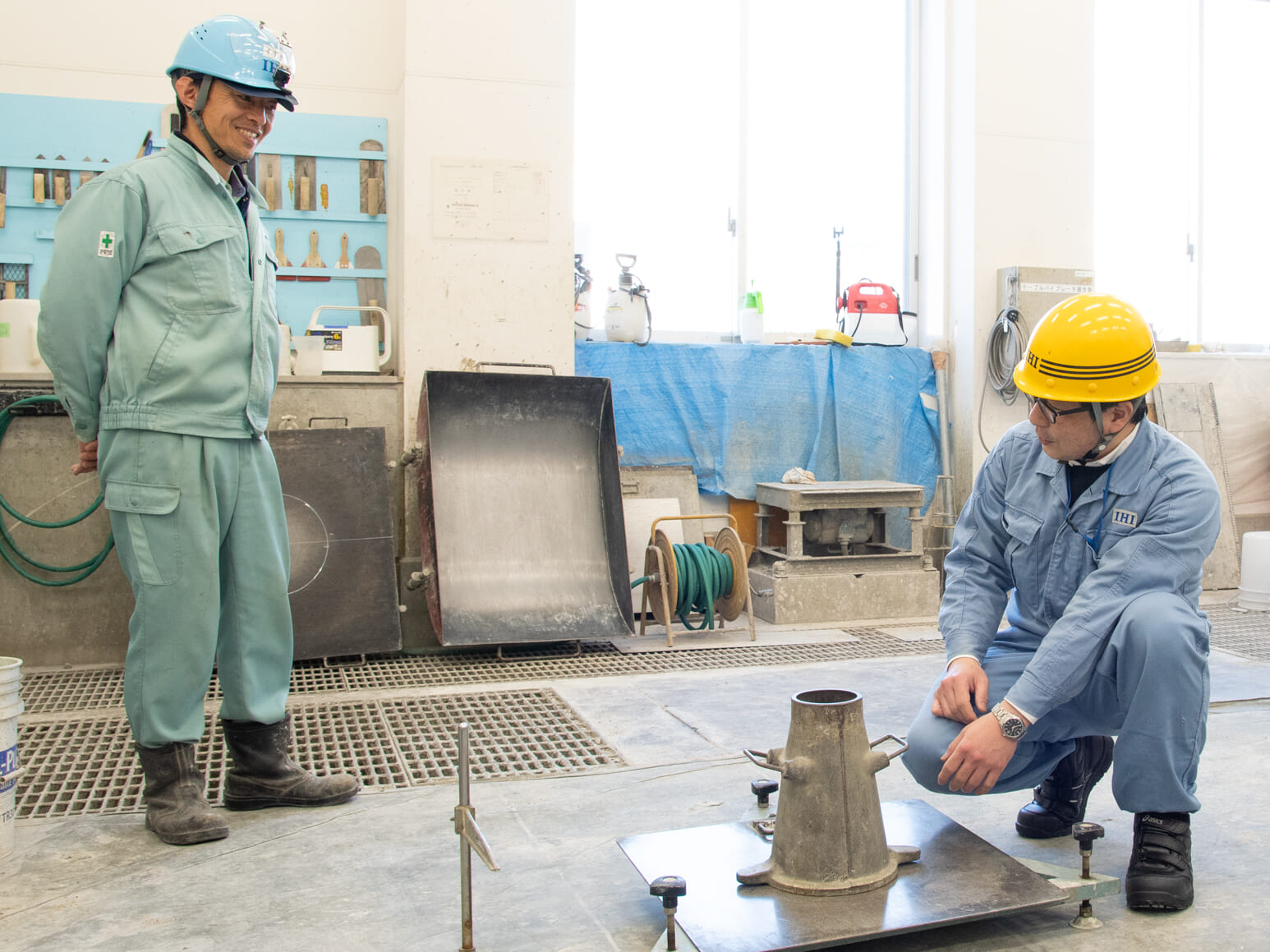
“I knew that because geopolymer is a highly viscous material, it is difficult to pump it over long distances. Therefore, it would be better to use the material for prefabrication rather than using it onsite, and that’s where IKK excels because they manufacture precast concrete products, such as shield tunnel liner segments. IHI already had experience working with IKK in large-scale projects. So, it was natural to approach them.” In response, IKK formed a carbon neutrality project team consisting of personnel from its design, manufacturing, public relations, and sales departments.
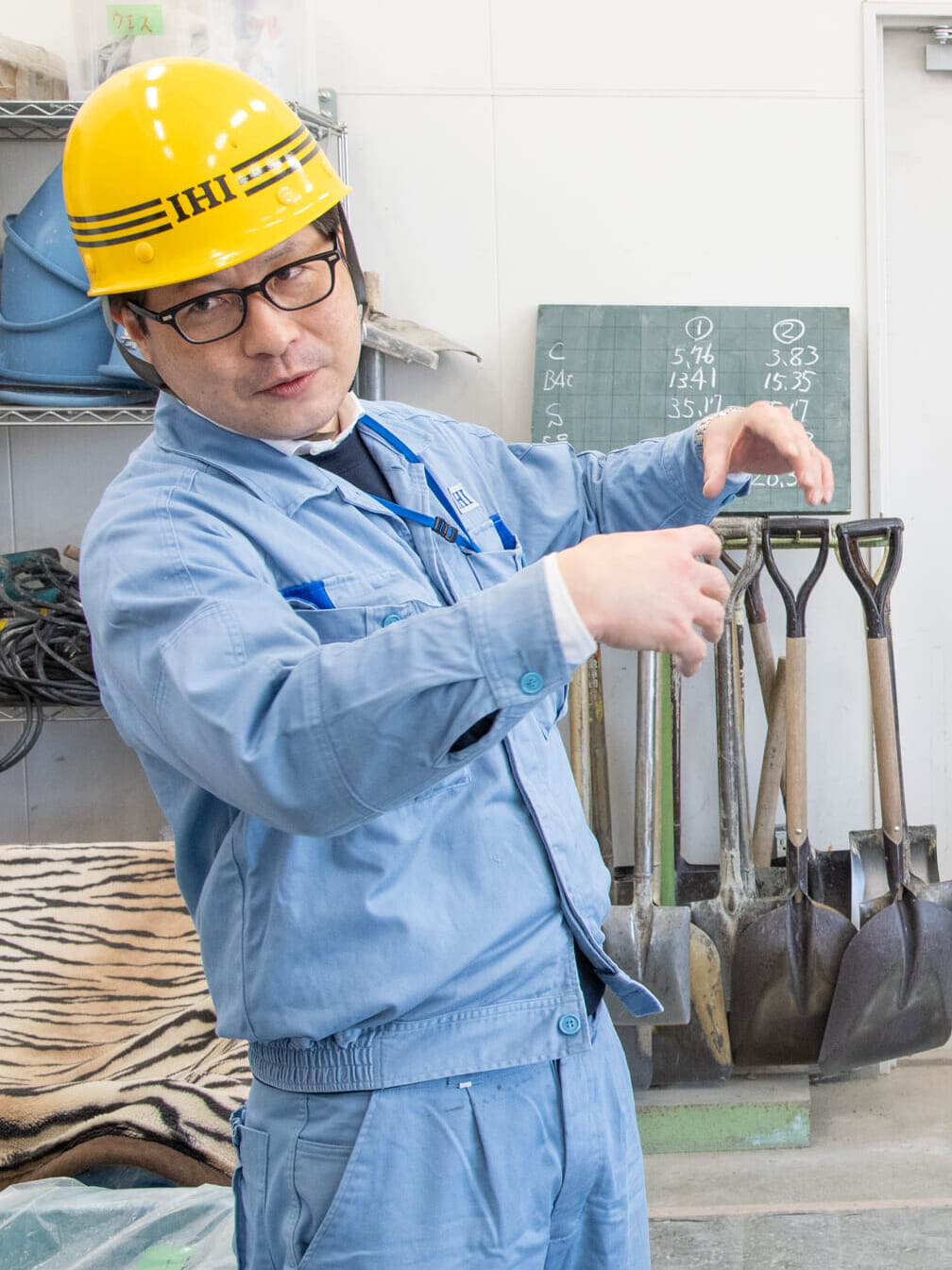
Kisaku also approached Professor Fujiyama of Yokohama National University, a concrete expert who was then researching geopolymer concrete, and asked her to join the project. Four-party research thus began in April 2022.
The goals set at that time were to achieve the performance goal and to file three patent applications by the end of June. “I asked team members to make one trial product a week and evaluate it. I knew it was too demanding, and we ended up quarreling on some occasions,” Kisaku confessed. The goal, needless to say, was not without reason. “My instincts, as a leader, told me that the project would not be successful unless we worked at such a pace for the first two or three months.”
Hiroya Suzuki, Research and Experiment Center, Development Department, Engineering Headquarters, IKK, who has been involved in cement research and testing for nearly 20 years, reflected on his involvement: “I did my best to meet the progress requirements set by Kisaku-san because I undertook his unreasonable assignments. It’s easy to say ‘once a week,’ but completing a testing cycle is truly hard work. Adjusting the moisture content of aggregates (gravel and sand), preparing materials and batching in advance, and mixing them in a mixer and checking on fluidity and everything—meanwhile fabricating specimens for strength testing,conducting strength tests, sorting out and feeding back the results so that the next mix specifications can be determined, and preparing a new set of materials for the next cycle in view of newly specified mix requirements. Particularly during the initial stage, repeating that cycle was really challenging to say the least.”
According to Suzuki, the differences from cement concrete were another challenge. “The alkalinity is so high that geopolymer paste contacting with the skin may cause the skin to peel. So, it required more careful handling than cement. We could not use the conventional wastewater treatment method. We had to formulate special flocculants and introduce new devices for flocculation and precipitation followed by pH adjustment before releasing any wastewater. This was no easy task indeed,” Suzuki noted.

Shunya Ikawa of Research and Experiment Center, Development Department, Engineering Headquarters, IKK, who participated in the project with Suzuki, recalled the difficulties they faced when actually conducting tests: “The testing methods and tools we use for cement are often not suitable for use with geopolymer, which is a silicon oxide-based material. It is sticky and sticks to the metal formwork, so we had a hard time leveling (smoothing the surface of) the geopolymer being cast because it significantly differs from cement.”
Ikawa said that the only way to overcome such problems is to “actually do it and see what happens.” “The first step is to conduct a test in accordance with the standard for cement. If the test results show something is wrong, try another method. We did that over and over again.” The project members gradually gained knowledge through trial and error, and it was, as Kisaku noted, the perfect example of the so-called San-Gen Principle (literally, the “Three Gen’s”—namely, Genba, which means actual place; Genbutsu, which means actual objects; and Genjitsu, which means the facts). A symbolic event occurred during the project.
When the project team was testing newly developed mixes, the test results suddenly began to show low strength values. Kisaku explained: “Some members suspected that Ikawa had made a mistake in measuring the quantities of the materials.” After a number of reviews and verifications, they finally found that the results were due to the differences between the materials used in different lots. Kisaku apologized for having doubted Ikawa’s abilities. Kisaku continued: “However, it was really difficult to identify the cause of the problem because there were too many things to consider, such as preparing and testing both coarse-grained powders and fine powders.”
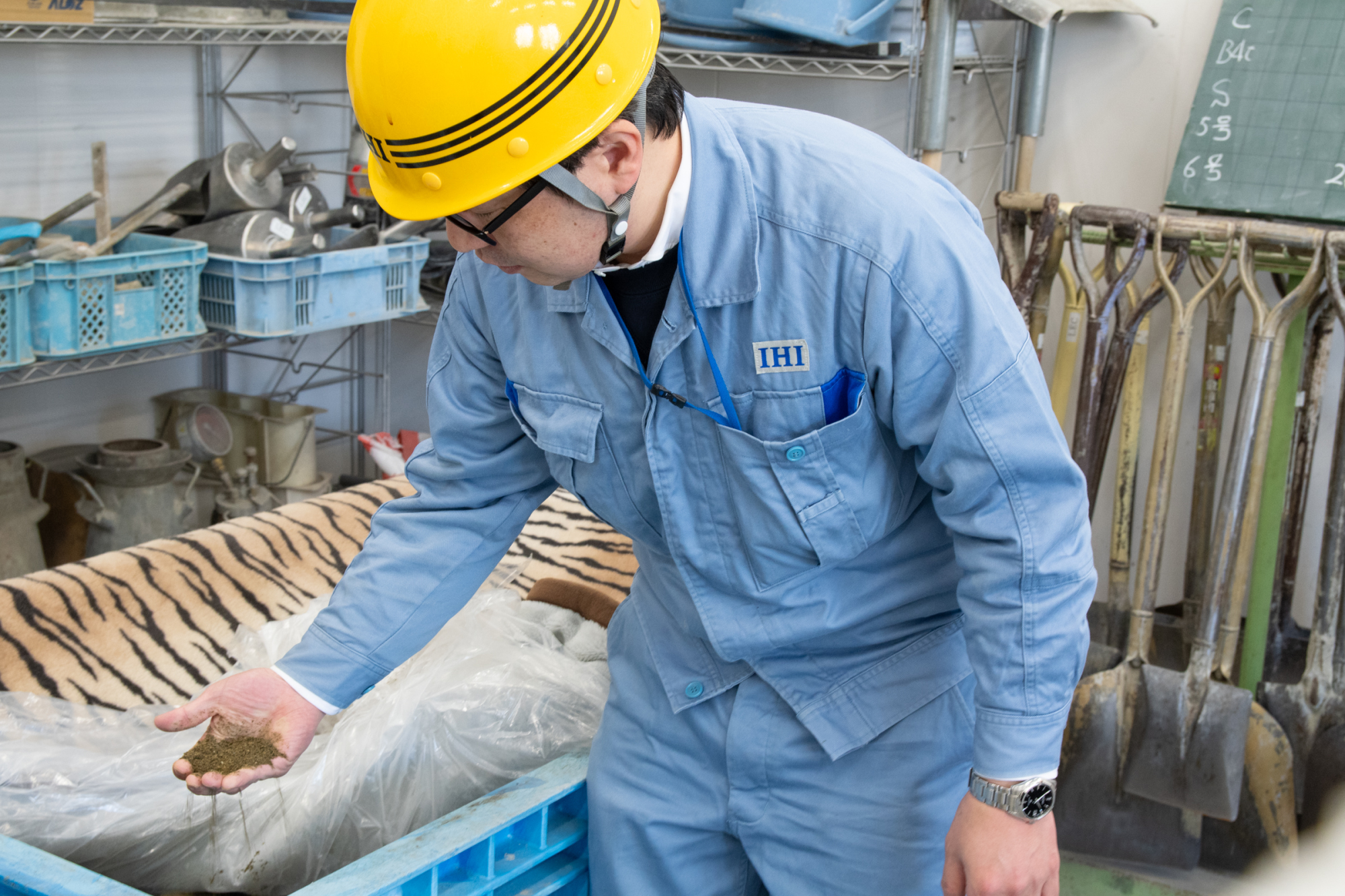
CEMENON was finally released after overcoming such numerous difficulties and achieving the challenging goals set at the start, in just one year from starting the project. Yuki Yoshida, Material and Structural Engineering Department, Technology Platform Center, Corporate Research & Development Division, recollected: “Though abundant knowledge regarding cement concrete has been accumulated over many years, we knew practically nothing about geopolymer concrete. We were required to show our ability to decide what to take and what to leave as well as to decide what is and is not important within the limited amount of time were put to test.”
CEMENON contains metakaolin as its alumina-silica powder. This resulted in one characteristic of CEMENON that it is about 15 times more acid-resistant than cement concrete. It was important to decide which to select as the advantageous characteristics of CEMENON from the number of potential directions and possibilities: “As the first step, it was necessary to conduct exhaustive tests and then decide which performance attributes to pursue. It was the kind of judgment that I was not able to make on my own; the team members’ intuitions are what made such decision making possible,” Yoshida noted.
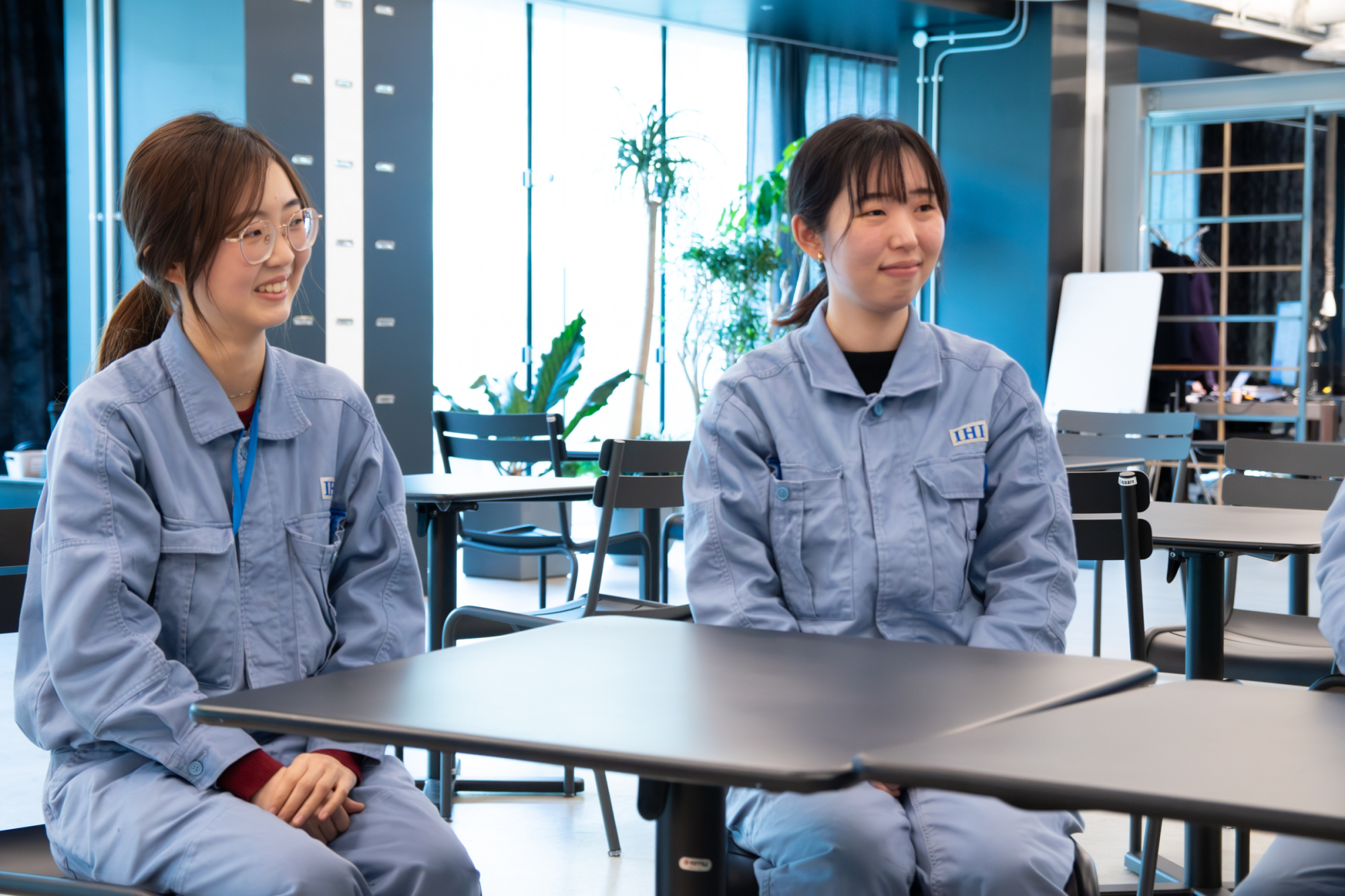
Kisaku added: “As Yoshida-san says, there are as many as 400 or 500 things that we could do if we tried, but actually the most we can do is 10 or so because of our limited human resources and time. Deciding which to pursue, therefore, is of crucial importance.
Without selecting straight routes in as many choices as possible,
, we would not be able to reach our goal quickly.” “The greatest challenge was that we couldn’t afford to turn back because of time constraints. It was quite difficult to decide which way to lead our team members from among the unlimited number of ways we could have gone.”
Kisaku said that he had a hard time persuading the various people involved. “There are many of those having strong character in the Corporate Research & Development Division, and IKK personnel tend to have a strong sense of craftsmanship, which can make them persistent. Salespeople are bound by business-related constraints, while ADVAN ENG has a team of engineers with strongly held sensibilities. It was truly a challenge to win over and coordinate with such tough people and work as a team,” Kisaku said with a warm smile, after which he added quietly, “although I’m still having a hard time.”
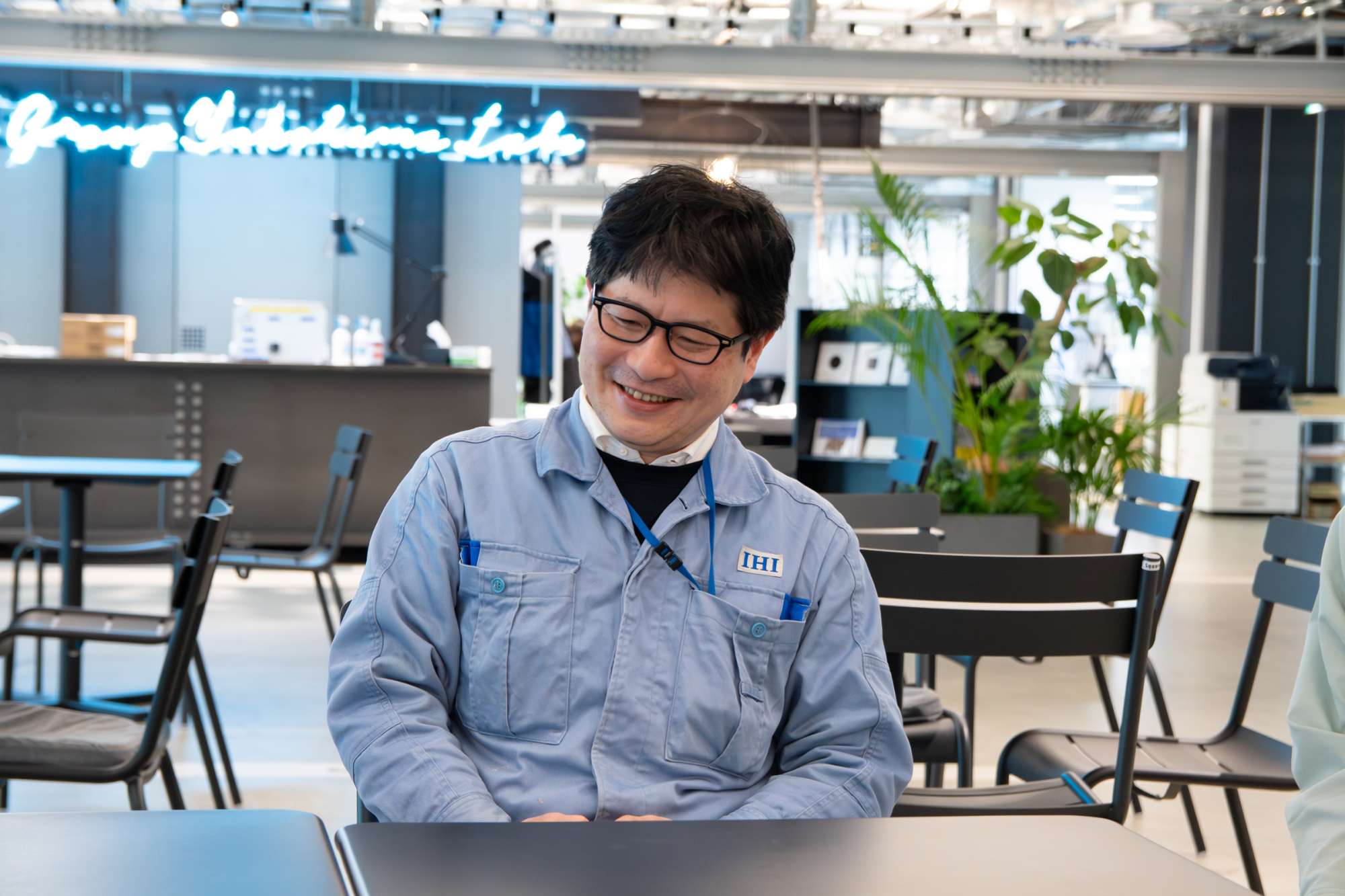
Special thanks:
Tomoaki Kisaku | Product and Process Transformation Group, Engineering Department, Integrated Development Center, Corporate Research & Development Division (At the time of the interview)
Yuki Yoshida | Material and Structural Technology Department, Technology Platform Center, Corporate Research & Development Division (At the time of the interview)
Jing Nie | Material and Structural Technology Department, Technology Platform Center, Corporate Research & Development Division
Hiroya Suzuki | Research and Test Center, Engineering Division, IHI Construction Materials Co ., Ltd
Shunya Ikawa|Research and Test Center, Engineering Division, IHI Construction Materials Co ., Ltd